BSR-050 Hydrogen Sulfide Removal Media
A new solution for H2S removal
Operators of landfills, waste water treatment plants, and digesters now have a new choice for solving their H2S removal problems. Guild Associates, Inc. is proud to introduce BSR-050 – a high capacity, fast-acting mixed metal oxide, engineered to remove hydrogen sulfide from waste gas.
Like Iron Sponge media, BSR-050 media has integral catalytic sites to enable a sequence of reactions to convert the H2S to elemental sulfur. In Iron Sponge media, these reactions only occur on the surface of the pellet; BSR-050 media, however, has a pore structure that enables this reaction to occur not only on the external surface, but thoughout the internal volume of the pellet. Utilizing the entire volume instead of only the pellet surface enables the BSR-050 media to achieve industry-leading H2S removal on a pound-per-pound basis. As a consequence, BSR-50 offers unprecedented benefits to the operator:
- The highest pound of H2S removed per pound of media in the industry
- Fast media removal with vacuum truck
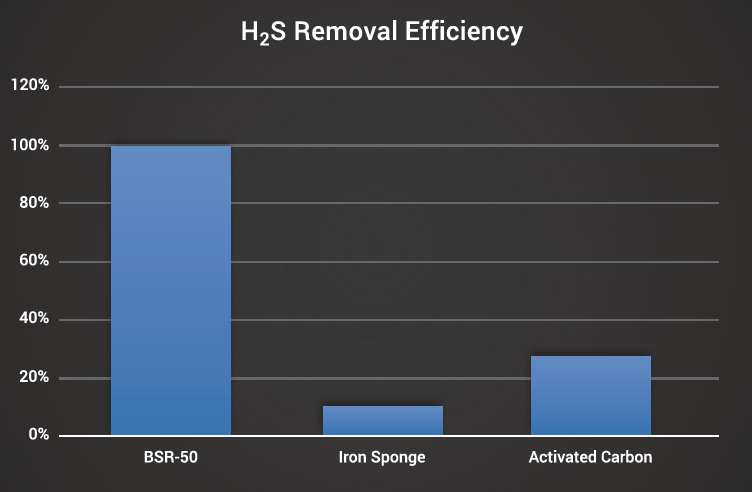 BSR-050 Removal Capacity Far Exceeds Iron Sponge and Activated Carbon Technologies | Note the comparison to the left of BSR-050 Removal Capacity to Iron Sponge and Activated Carbon. BSR-050 is compatible with most existing process vessels, so the media can likely be utilized with existing equipment. For new installations, the high capacity and long life characteristics of the media can enable smaller vessels, thus reducing initial capital expenditure. Operational costs are lowered by the less-frequent media changes and less electrical load resulting from varying pressure drop in the bed.
|
A useful feature of BSR-050 is the color change of spent media, as illustrated in the picture to the right.
Pilot-scale tests at a landfill site have proved the media's performance under real-world conditions. BSR-050 media was subjected to landfill gas containing 600-900 PPM H2S over a 43-day period. The vessel was sized for treatment using 3.8 lbs of BSR-050 per SCFM of feed gas, compared with the landfill's existing system which utilized 20 lbs of carbon media per each SCFM. The effluent flow was measured at undetectable levels of H2S until day 40, and the test was stopped at day 43 when effluent flow reached 90 PPM. |
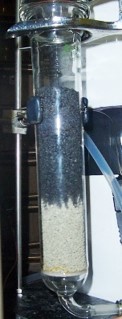 Sharp Color Change Indicative of Fast Acting Media |
Analysis of spent media verified that the H2S removal capacity exceeded 1.0 lb/lb. Further, the spent media was analyzed by an independent laboratory for hazardous material using “Test Methods for Evaluating Solid Waste,” USEPA Document SW 846 (February, 2007)" and found to be classified as non-hazardous waste.
BSR-050 media is fully validated and is being manufactured at high volume in a new Guild Associates, Inc. facility. Contact Guild Associates for a quotation on a system or replacement media. Our H2S specialists are ready to evaluate your application and design a process that maximizes the performance of BSR-050 media for your gas treatment needs.
Do you have a project in mind? Download our
CUSTOMER QUESTIONNAIRE and send the completed form to Guild Associates. If you have questions or want to discuss your specific application, contact Paul Baker at 614-760-8013 or email to at
Information Requests.
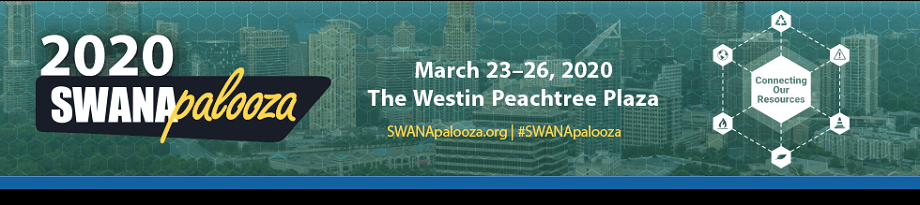
Come See Us At SWANApalooza 2020, Booth #335!
Dr. Joseph A. Rossin, VP of Materials Development at Guild Associates, will be a panelist for the "Hydrogen Sulfide Removal: Exploring New, More Efficient Technologies and Methods" session at the SWANAPalooza 2020 conference in Atlanta, GA. Dr. Rossin's presentation will focus on understanding hydrogen sulfide removal as a complete process to reduce the total cost of operation for disposable media applications.
Talk: Hydrogen Sulfide Removal: Exploring New, More Efficient Technologies and Methods
Panelist: Dr. Joseph A. Rossin, Guild Associates VP of Materials Development
When: Tuesday, March 24, 2020: 3:00 PM - 3:45 PM
Full session details